1. COMPOSITES ARE SUPER STRONG
Carbon rods are stiffer than steel and resistant to fatigue and wear. Pultruded carbon and fiberglass are designed to be strong in a specific direction and wrapped composite tubes can be designed to have incredible hoop strength and impact resistance.
2. COMPOSITES ARE LIGHTWEIGHT
You can quickly reduce the weight of your product by replacing steel or other metal rods and tubes with carbon or fiberglass. Carbon is 5x lighter than steel and almost 2x lighter than aluminum.
3. COMPOSITES ARE RESISTANT TO ENVIRONMENTAL CHANGES
Is humidity a factor in your product? What about temperature fluctuations or corrosion? Temperature and moisture have very little effect on carbon and fiberglass, so you can count on your product attributes, such as size and strength, remaining unchanged whether it is hot or cool, wet or dry.

4. GOODWINDS COMPOSITES STOCKS A VARIETY OF SIZES FOR FAST PROTOTYPING.
We offer off-the-shelf sizes ranging from .020” to .750” in diameter for our carbon and fiberglass rods and tubes. We have no minimum orders and we are happy to cut your composite rods and tubes to your specification at no charge.
5. GOODWINDS COMPOSITES MAKES CUSTOM RODS AND TUBES
Our engineers can design a wrapped carbon tube to meet your exact specifications, from diameter and wall thickness to stiffness and hoop strength. We custom pultrude micro carbon rods from .020” to .125” in diameter
6. COMPOSITE RODS AND TUBES ARE MACHINABLE.
Goodwinds Composites precision machines carbon and fiberglass rods and tubes to tight tolerances. We can grind to a specific outer diameter, cut to within .005”, mill, drill, chamfer, sand, and many other secondary processes.NASA and Goodwinds
7. COMPOSITES ARE TRULY SPACE AGE!
In the past ten years, composites have completely transformed the aerospace industry, allowing us to go farther, faster, using less fuel. Consumer goods, industrial machinery, construction, automotive, energy, and so many more industries have left traditional materials behind in favor of composites.
Composites have the power to transform your products and the way you manufacture them. Goodwinds Composites can help find the right carbon and fiberglass rods and tubes for your applications.
When NASA flies its first Mars helicopter on the red planet in 2021, Goodwinds Composites will share in that history.

LOCAL COMPANY HELPS WITH NASA MARS HELICOPTER PROJECT
July 3, 2019
MOUNT VERNON — When NASA flies its first Mars helicopter on the red planet in 2021, Mount Vernon company Goodwinds Composites will share in that history.
The company helped engineer and manufactured the wrapped carbon tubes for the landing gear of the 4-pound, unmanned helicopter, said co-owner Amelia Cook.
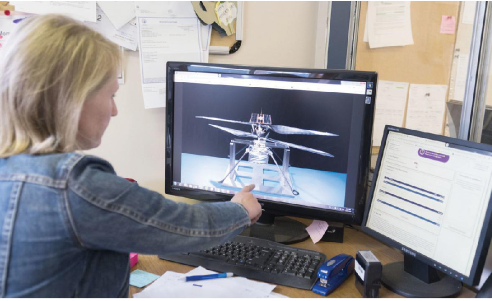
Goodwinds Composites co-founder Amelia Cook shows a rendering of the NASA Mars exploration drone.
PHOTO: CHARLES BILES / SKAGIT VALLEY HERALD
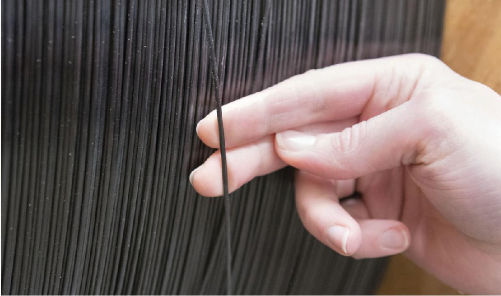
Amelia Cook explains the properties of flexible, narrow guage carbon fiber tubing June 21 at Goodwinds Composites in Mount Vernon, Wash.
PHOTO: CHARLES BILES / SKAGIT VALLEY HERALD
Cook and brother Leland Holeman opened the business in 2008, and make carbon fiber and fiberglass tubes and rods. NASA contacted the company about a year ago about working on the helicopter project, Cook said.
“It will be really cool to say something we manufactured went to Mars,” she said. The helicopter, which is undergoing its final phase of testing, is scheduled to launch in July 2020 with land vehicle the Mars rover, and reach the planet in 2021.
The helicopter will be the first heavier-than-air vehicle to fly on Mars, which has an atmosphere thinner than Earth’s, according to a June article from NASA’s Jet Propulsion Laboratory.
The helicopter may be used in future missions to access hard-to-reach places and obtain aerial images.
Cook said demand is growing for composites such a carbon fiber, which is made from carbon fiber strands and a binding agent. Carbon fiber has advantages in that it is lightweight and durable, she said.
The company’s machines can cut to specific width and thickness, and create carbon tubing as thin as wire.
“Anywhere weight is a factor is where carbon is becoming the norm,” Cook said.
Applications include aerospace and medical equipment and high-end hobbies such as model airplanes. Cook said the company has more orders than it can fill at the moment.
The company hopes to add four employees to its 11-person crew by the end of summer and eventually expand into a larger building, she said.
Cook said the company wouldn’t hesitate to work on another NASA project.
“It’s great to be innovative and getting inquiries from customers like NASA,” she said.
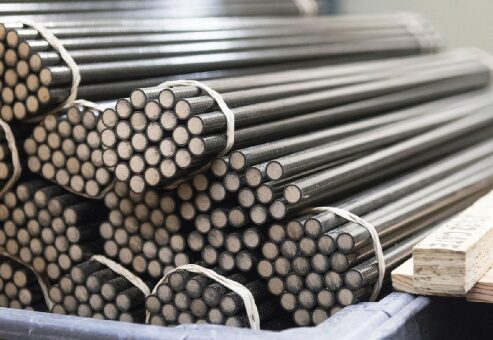
Bundles of 25-count carbon fiber rods await shipment to clients June 21 at Goodwinds Composites in Mount Vernon, Wash.
PHOTO: CHARLES BILES / SKAGIT VALLEY HERALD
— Reporter Jacqueline Allison: [email protected], 360-416-2145, Twitter: @Jacqueline_SVH
Additional images at: https://www.goskagit.com/news/local_news/local-company-helps-with-nasa-mars-helicopter-project/article_722741c2-7747-52e8-bec6-57e333101ec0.html